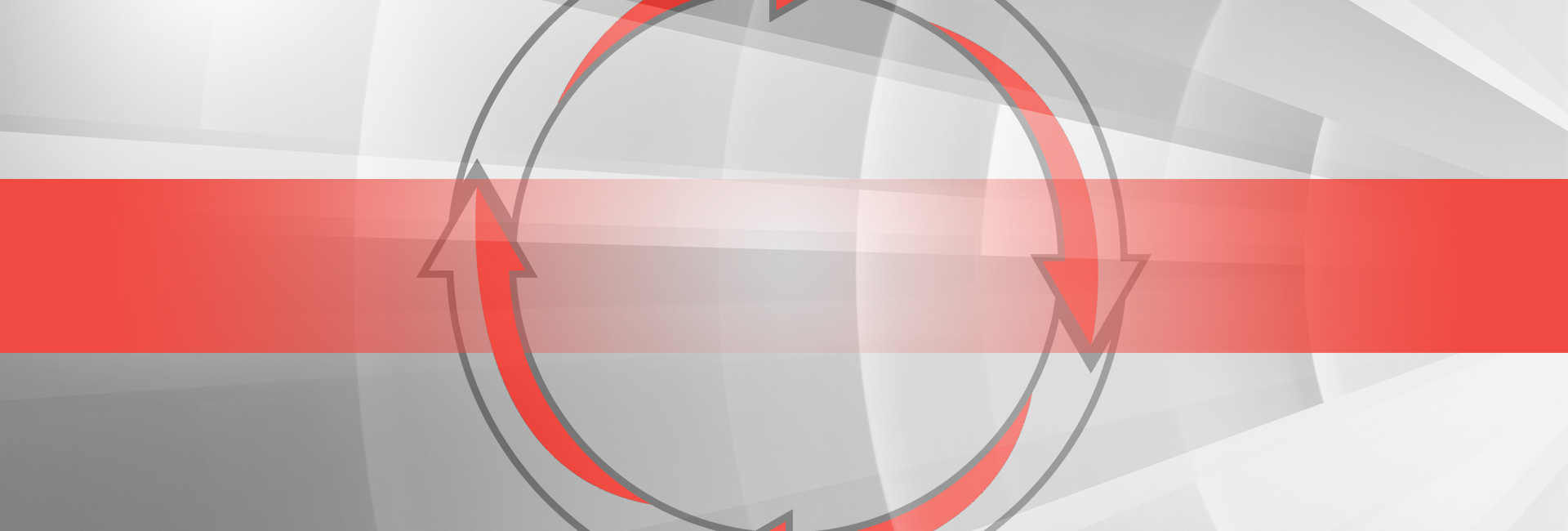
Our repair process
Shipping
Please send us your spindle together with your order or a description of the failure. To save time, you can complete our online repair form, indicating defects and problems observed. You'll automatically be assigned a number. Our customer service will be informed about the imminent arrival of your spindle and thus be in a position to anticipate and check if critical parts such as bearings, sensors or motors are available in stock.
You can print this form and join it to your spindle. All inquiries are recorded and you have the possibility to consult them at any time on myRenaud (login and password on demand).
Inspection on arrival
Upon arrival at Robert Renaud SA, your spindle will be entered in our computer system and assigned a job number. We'll adress you an e-mail or fax confirming you its arrival and indicating the job number.
Our service specialists will proceed to a first analysis of your spindle, testing in particular the motor and cabling and controlling the geometry with equipments allowing measures in the micrometer tolerance. Furthermore, and if the state of your spindle allows it, we'll check vibrations rate and noise of the bearings, and also control sensors, clamping system, cooling system and air barrier. If necessary, fotos will be taken. All tests will be registered in our data base.
Our service team will contact you, should it prove necessary to replace other parts than the bearings. On demand you'll receive a quote with the confirmation of the delivery date. We'll proceed to the repair of your spindle at receipt of your approval.
Disassembly of the spinde
Our specialists will disassemble and carefully clean all parts of your spindle. Main parts such as shaft, bearings and housing will be controlled meticulously in our metrology department, where a high-tech laboratory allows dimensional and forms measurement of concentricity, coaxiality, etc., in the nanometer tolerance. Should any of the measured parts not meet the tolerances and need replacing, you'll be contacted by our service team. If these parts are not available at our stock, we are in a position to manufacture them in-house with our CNC-machines of the latest generation.
Re-assembly of the spindle
The spindle will be re-assembled same way as a new spindle. Controlling of the force of the new bearings and of the various tolerances in the micrometer tolerance necessary for proper functioning of the spindle will be executed with great care. Some of the parts will be balanced individually before assembly. After assembly, the whole spindle will be balanced again and numerous controls such as testing of sensors, electrical cables, pneumatic or hydraulic clamping system, clamping force, cooling system, air flow, final geometry of the spindle, measuring of the temperatures, vibrations rate and noise of the bearings will be done.
We will run the spindle on our test benches according to the guidelines and to up to maximum speed. All these tests are recorded and saved in our data base. A final test protocol approved by the department head will be provided together with the spindle. To ensure a pefect follow-up, these protocols can be viewed at any time on myRenaud. A digital copy can be saved and avoids any paper-related work.
Return shipment
After our service department released your spindle, it will be routed to our shipping department, where it will be equipped with the various caps and protections such as anti-rust paper or special film, to avoid pollution and humidity. Depending on the size of the spindle, we'll choose adequate packaging as cardboard boxes or special wooden crates to ensure worldwide safe delivery.